Original quality fuel injector assembly VG1560080276 for HOWO
The fuel injector is a precision device with very high processing accuracy, which requires a large dynamic flow range, strong anti-clogging and anti-pollution capabilities, and good atomization performance. The fuel injector receives the injection pulse signal sent by the ECU and accurately controls the amount of fuel injection.
The electronic fuel injector is the most critical and complex component in the common rail system, and is also the most difficult component to design and process. The ECU controls the opening and closing of the solenoid valve to inject the fuel in the high-pressure rail into the combustion chamber with the best injection timing, injection amount and injection rate. In order to achieve an effective injection start point and accurate injection amount, the common rail system uses a special fuel injector with a hydraulic servo system and an electronic control element (solenoid valve).
The fuel injector consists of a hole-type fuel injector, a hydraulic servo system (control piston, control orifice, etc.), and a solenoid valve, which are similar to traditional fuel injectors.
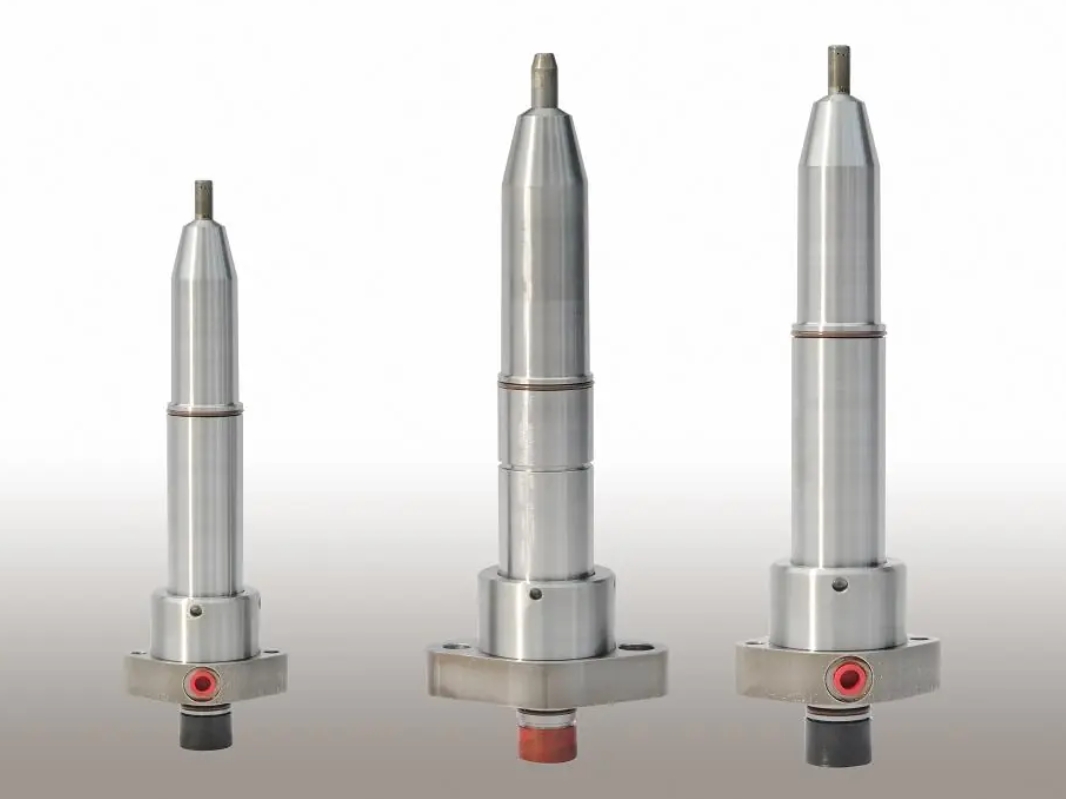
Work Theory
The diesel engine fuel injection system atomizes the fuel and distributes it in the combustion chamber to mix with the air. It mainly consists of the fuel injection nozzle and the injector body. Its installation position and angle on the cylinder head depend on the design of the combustion chamber.
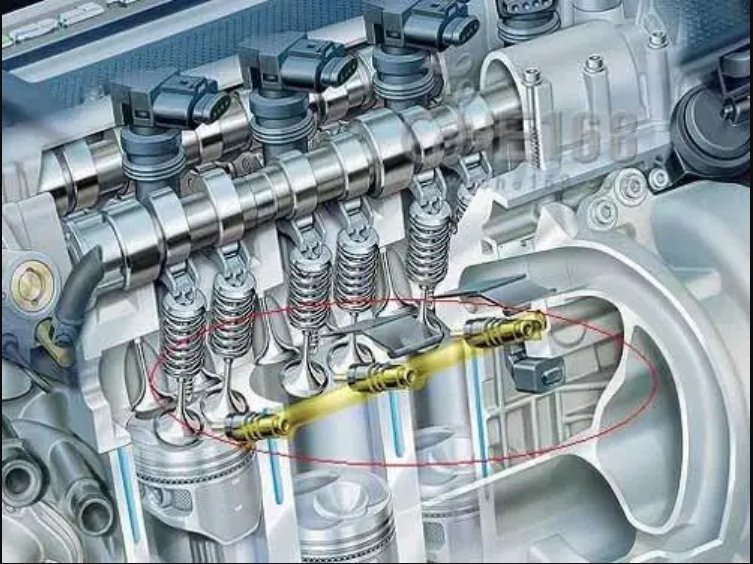
There are two types of fuel injectors: open and closed. The open fuel injector has a simple structure, but poor atomization and is rarely used. The closed fuel injector is widely used in various diesel engines. The diesel engine inhales pure air during the intake stroke. When the compression stroke is close to the end, the diesel oil is increased to more than 100MPa by the injection pump, and is sprayed into the cylinder through the injector. In a very short time, it mixes with the compressed high-temperature air to form a combustible mixture. Due to the high compression ratio of the diesel engine (generally 16-22), the air pressure in the cylinder at the end of compression can reach 3.5-4.5MPa, and the temperature is as high as 750-1000K (while the mixed gas pressure of the gasoline engine at this time will be 0.6-1.2MPa, and the temperature will reach 600-700K), which greatly exceeds the auto-ignition temperature of diesel. Therefore, after the diesel is sprayed into the cylinder, it will ignite and burn immediately after mixing with the air in a very short time. The gas pressure in the cylinder rises rapidly to 6-9 MPa, and the temperature rises to 2000-2500 K. Driven by the high-pressure gas, the piston moves downward and drives the crankshaft to rotate to perform work, and the exhaust gas is also discharged into the atmosphere through the exhaust pipe.
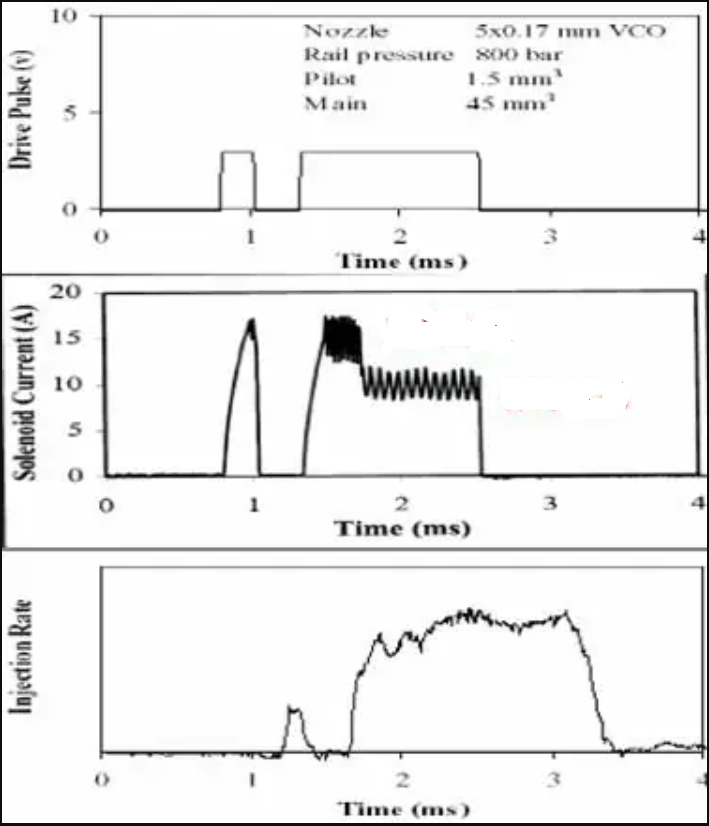
Maintenance
The injector should be checked and adjusted once every 700 hours. If the opening pressure is lower than the specified value by more than 1Mpa or the needle valve head is seriously carbonized, the needle valve should be removed and placed in clean diesel, and the carbon deposits should be scraped off with wood chips, and the spray hole should be cleared with a thin steel wire. After installation, it should be debugged. The injection pressure difference of each cylinder of the same machine must be less than 1Mpa.
In order to ensure that the diesel injected into the cylinder by the injector can be burned completely and in time, the fuel supply time of the fuel pump must be checked regularly. If the fuel supply time is too early, the vehicle will have difficulty starting and knocking failures; if the fuel supply time is too late, it will cause black smoke from the exhaust, high engine temperature, and increased fuel consumption.
The matching precision of the injector needle valve pair is extremely high, and the spray hole diameter is very small, so the specified brand of clean diesel must be selected strictly according to seasonal changes, otherwise the injector will not work properly.
When cleaning the injector needle valve pair, do not collide with other hard objects, and do not let it fall to the ground to avoid scratches. When replacing the injector needle valve pair, first put the new pair into 80℃ hot diesel and soak it for about 10 seconds to allow the anti-rust oil to fully dissolve, then pull the needle valve back and forth in the valve body in clean diesel to clean it thoroughly, so as to avoid the needle valve sticking due to the dissolution of the anti-rust oil when the injector is working.
Function
1. Increase oil pressure (constant pressure): Increase the injection pressure to 10MPa~20MPa.
2. Control the injection time (timing): Inject and stop the injection at the specified time.
3. Control the injection amount (quantity): Change the injection amount according to the working condition of the diesel engine to adjust the speed and power of the diesel engine.
Requirements
1. Supply fuel according to the working order of the diesel engine, and the fuel supply to each cylinder is uniform.
2. The advance angle of fuel supply to each cylinder must be the same.
3. The duration of fuel supply to each cylinder must be equal.
4. The establishment of oil pressure and the stopping of fuel supply must be rapid to prevent dripping.
Troubleshooting Methods
1. Very little fuel is injected or no fuel is injected:
(1) There is air in the fuel system oil circuit. Remove the air in the high-pressure or low-pressure oil pipe.
(2) The injector parts are stuck. Repair or replace.
(3) The fuel pump is not supplying fuel normally. Find out the cause and deal with it according to the troubleshooting method of the injector pump.
(4) The high-pressure oil pipe is leaking. Tighten the nut. If there is a crack in the oil pipe, it should be replaced.
(5) The injector parts are worn. Replace or repair.
2. Low injection pressure:
(1) The pressure regulating screw is loose. Readjust to the specified pressure as required and tighten the lock nut.
(2) The pressure regulating spring is deformed. Adjust or replace.
(3) The needle valve is stuck. Clean or grind.
(4) The spring seat, push rod and other parts are worn. Repair or replace.
3. Too high injection pressure:
(1) The pressure regulating spring has high elasticity. Readjust to the specified pressure as required and tighten the lock nut.
(2) The needle valve is stuck. Clean or grind.
(3) The spray hole is blocked. Clean the spray hole or replace the nozzle.
4. Injector oil leakage:
(1) The pressure regulating spring is broken. Replace with a new spring
(2) The seat surface of the needle valve body is damaged. Replace
(3) The needle valve is stuck. Clean, grind or replace
(4) The cap is deformed. Replace
(5) The surface of the injector body is worn. Grind or replace
5. Poor injection atomization:
(1) The injection pressure is low. Adjust to the specified pressure.
(2) The seat surface of the injector nozzle is damaged or burned. Grind or replace.
(3) There is garbage on the mating surface of the injector nozzle. Clean it in time.
6. Injection line:
(1) The spray hole is blocked. Use a steel wire with a diameter of 0.2-0.3MM to clear the spray hole.
(2) The seat surface of the needle valve body is excessively worn. Replace a new needle valve body.
(3) The needle valve is stuck. Clean, grind or replace.
7. The surface of the needle valve is burned or blue-black (diesel engine overheating). Check the cooling system and pay attention to replacing the mating parts. Do not overload the diesel engine for a long time.
Maintain Methods
The fuel injector is one of the three pairs of precision parts in the fuel supply system of a diesel engine. Its normal service life is more than one thousand hours. However, due to improper use, it is often worn out and stuck after hundreds of hours or even dozens of hours of use.
The main reasons for the nozzle to get stuck:
1. The diesel is not clean, and there are impurities in the high-pressure oil pipe, which makes the needle valve pair not close tightly, and the high-pressure gas in the combustion chamber is reversed, burning the needle valve pair. In addition, the dirt on the injector pressure regulating spring, tappet and other parts is moved to the upper part of the injector needle valve through the injector tappet, or the cotton rope and lead wire used to prevent oil leakage in the oil line enter the injector through the high-pressure oil pipe, which will cause the needle valve pair to get stuck.
2. The engine temperature is too high and the injector is poorly cooled, causing the needle valve pair to get stuck. However, too late fuel supply time, too much scale or blockage in the cooling water channel, wear on the end face of the water pump impeller, and long-term overload of the engine will cause the engine to overheat.
3. The oil outlet valve is worn, causing oil dripping when the injector stops injecting oil, which causes the nozzle to burn and accumulate carbon, resulting in a stuck fault.
4. When installing the injector, the gasket is not installed or the gasket is damaged, causing leakage, causing the local temperature of the injector to be too high and stuck.
5. The injection pressure is too low, causing the high-pressure gas in the combustion chamber to flow back.
6. Reasons in parts manufacturing, such as the injector mounting hole on the cylinder head is too tight with the injector, the gap between the needle valve body and the mounting hole on the cylinder head is too small, and the cylinder head injector mounting hole is processed too deep.
Repair method for stuck fuel injector:
First put the stuck fuel injector into diesel or engine oil to warm it up, then take it out and wrap it with cloth, then use pliers to clamp the needle valve and slowly move it to remove the needle valve from the needle valve body. Drop a small amount of clean engine oil into the needle valve body, so that the needle valve moves repeatedly in the needle valve body until the needle valve can move freely in the needle valve body. If there are traces of burns on the sealing surface of the needle valve, it should be ground with grinding paste. When grinding, pay attention to the amount of grinding paste and grinding time. Install the cleaned needle valve pair on the injector, and adjust the injection pressure before reuse.
Daily Maintenance
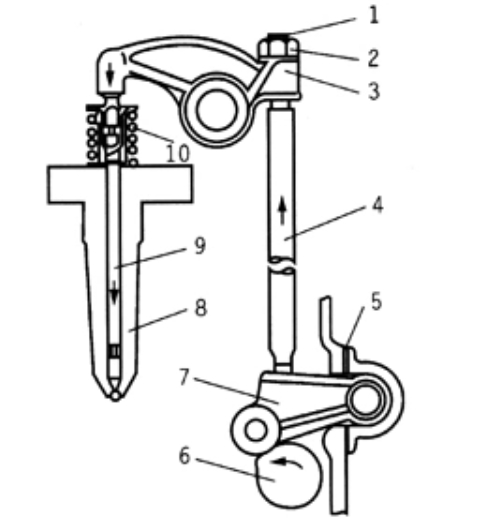
1. Properly maintain the accessories of the fuel injection pump
The pump body side cover, oil dipstick, refueling plug (breather), overflow valve, oil pool screw plug, oil plane screw, oil pump fixing bolt, etc. must be kept intact. These accessories play a vital role in the operation of the fuel injection pump. For example, the side cover can prevent the intrusion of impurities such as dust and water, the breather (with filter) can effectively prevent the oil from deteriorating, and the overflow valve ensures that the fuel system has a certain pressure without entering the air. Therefore, it is necessary to strengthen the maintenance of these accessories, and repair or replace them in time if they are damaged or lost.
2. Check the amount of oil in the fuel injection pump oil pool and its quality regularly to see if they meet the requirements.
Before starting the diesel generator each time, check the amount of oil in the fuel injection pump and its quality (except for the fuel injection pump that is forced to lubricate by the engine) to ensure that the amount of oil is sufficient and the quality is good. If the oil deteriorates due to mixing with water or diesel, it will cause early wear of the plunger and the oil outlet valve pair, resulting in insufficient power of the diesel engine and difficulty in starting. In severe cases, it will cause corrosion and rust of the plunger and the oil outlet valve pair. Due to internal leakage of the oil pump, poor operation of the oil outlet valve, wear of the oil pump tappet and housing, and damage to the sealing ring, diesel will leak into the oil pool and dilute the engine oil. Therefore, it should be replaced in time according to the quality of the engine oil. When replacing, the oil pool should be thoroughly cleaned and the sludge and other impurities at the bottom of the oil pool should be removed. Otherwise, the engine oil will deteriorate after a short period of use. The amount of engine oil should not be too much or too little. Too much oil in the governor can easily cause the diesel engine to "run away", and too little oil will cause poor lubrication. The oil dipstick or oil plane screw should be used as the standard. In addition, when the diesel engine is not used for a long time, be sure to check whether there are impurities such as water and diesel in the oil in the oil pump oil pool. If there are, replace it immediately. Otherwise, due to long-term storage, the water can easily cause the plunger and the oil outlet valve parts to rust and get stuck and become scrapped.
3. Regularly check and adjust the oil supply of each cylinder of the injection pump.
Due to the wear of the plunger and the oil outlet valve, diesel leakage will occur, which will reduce or uneven the oil supply of each cylinder, resulting in difficulty in starting the diesel engine, insufficient power, increased fuel consumption, and unstable operation. Therefore, it is necessary to regularly check and adjust the oil supply of each cylinder of the injection pump to ensure the power of the diesel engine. In actual use, the amount of oil supply of each cylinder can be determined by observing the exhaust of the diesel generator, listening to the engine sound, and touching the exhaust manifold temperature.
4. Use standard high-pressure oil pipes
During the oil supply process of the injection pump, due to the compressibility of diesel and the elasticity of the high-pressure oil pipe, high-pressure diesel will form pressure fluctuations in the pipe. It takes a certain amount of time for the pressure wave to be transmitted in the pipe. In order to ensure that the oil supply interval angle of each cylinder is consistent, the oil supply is uniform, and the diesel engine works smoothly, the length and diameter of the high-pressure oil pipe are selected after measurement. Therefore, when the high-pressure oil pipe of a cylinder is damaged, it should be replaced with an oil pipe of standard length and diameter. In actual use, due to the lack of standard oil pipes, other oil pipes are used instead, regardless of whether the length and diameter of the oil pipes are the same, resulting in a large difference in the length and diameter of the oil pipes. Although they can be used in an emergency, they will cause the advance angle and oil supply of the cylinder to change, causing the whole machine to work unsteadily. Therefore, standard high-pressure oil pipes must be used in use.
5. Check the sealing condition of the valve pair regularly.
After the injection pump has been working for a period of time, the wear of the plunger and the working condition of the oil pump can be roughly judged by checking the sealing condition of the oil valve, which is conducive to determining the repair and maintenance methods. During the inspection, unscrew the high-pressure oil pipe joints of each cylinder and pump oil with the hand oil pump of the oil pump. If oil is found to flow out of the oil pipe joint at the top of the injection pump, it means that the oil valve is not well sealed (of course, this situation will also occur if the oil valve spring is broken). If multiple cylinders have poor sealing, the injection pump should be thoroughly debugged and maintained, and the pair should be replaced.
6. Replace the worn plunger and oil outlet valve parts in time
When the diesel engine is difficult to start, power is reduced, and fuel consumption increases, and there is no improvement after adjusting the injection pump and injector, the injection pump plunger and oil outlet valve parts should be disassembled and inspected. If the plunger and oil outlet valve are worn to a certain extent, they should be replaced in time and do not insist on using them again. The losses caused by the wear of the parts, such as the difficulty in starting the diesel engine, increased fuel consumption, and insufficient power, far exceed the cost of replacing the parts. After replacement, the power and economy of the diesel engine will be significantly improved, so the worn parts should be replaced in time.
7. Keep a good control on the use and filtration of diesel to ensure that the diesel entering the injection pump is highly clean
Generally speaking, the filtration requirements of diesel generators for diesel are much higher than those of gasoline engines for gasoline. When using, diesel of the required brand should be selected and at least 48 hours of sedimentation should be allowed. Strengthen the cleaning and maintenance of the diesel filter, clean or replace the filter element in time; clean the diesel tank in time according to the working environment conditions, and thoroughly remove the sludge and water at the bottom of the tank. Any impurities in the diesel will cause serious corrosion or wear to the injection pump plunger, the oil delivery valve pair and the transmission parts.
8. Regularly check and adjust the injection pump fuel supply advance angle and the fuel supply interval angle of each cylinder
During use, due to the loosening of the coupling bolts, the wear of the camshaft and the roller body parts, the fuel supply advance angle and the fuel supply interval angle of each cylinder often change, causing the diesel combustion to deteriorate, the power and economy of the diesel engine to deteriorate, and at the same time, it is difficult to start, the operation is unstable, and abnormal noise and overheating are emitted. In actual use, most drivers pay attention to the inspection and adjustment of the overall fuel supply advance angle, but ignore the inspection and adjustment of the fuel supply interval angle (involving the adjustment of the single pump fuel supply advance angle). As a result, although the first cylinder is fueled at the right time after the overall adjustment, the fuel supply of the remaining cylinders is not necessarily at the right time due to the wear of the camshaft and roller transmission components. This will also cause the diesel engine to start with difficulty, lack of power, and unstable operation. Especially for the injection pump that has been used for a long time, it is more important to pay attention to the inspection and adjustment of the fuel supply interval angle.
9. Check the camshaft clearance regularly
The axial clearance of the injection pump camshaft is very strict, generally between 0.03 and 0.15mm. If the clearance is too large, it will aggravate the impact of the roller transmission components on the cam working surface, thereby increasing the early wear of the cam surface and changing the fuel supply advance angle; the camshaft bearing axial and diametrical clearance is too large, which can easily cause the camshaft to run unsteadily, the oil quantity adjustment lever to shake, and the fuel supply to change periodically, making the diesel engine run unsteadily. Therefore, regular inspection and adjustment are required. When the camshaft axial clearance is too large, you can add gaskets on both sides to adjust it. If the radial clearance is too large, it is generally necessary to replace it with a new one.
10. Regularly check the wear of the relevant key slots and fixing bolts.